When selecting the perfect control arm material for automotive applications, understanding the composition and benefits of different materials is essential for optimizing vehicle performance. Car enthusiasts, automotive engineers, and manufacturers alike seek not only cost-effective solutions but also those that enhance durability, safety, and drive quality.
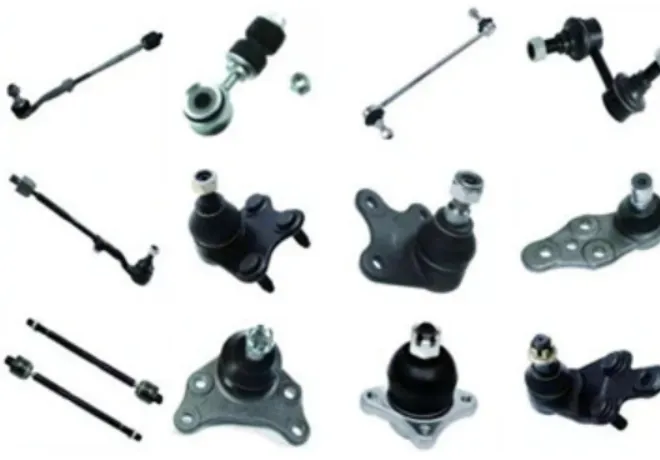
Aluminum is a top contender in the realm of control arm materials due to its lightweight nature. While lighter, it maintains immense strength, making it a favorite in the racing and high-performance automobile industries. The reduced weight of aluminum not only enhances vehicle fuel efficiency but also improves handling by allowing for more responsive steering. The material's ability to withstand corrosion further enhances its longevity, ensuring vehicles maintain peak performance over longer periods.
Steel, on the other hand, has long been the traditional choice, renowned for its robustness and affordability. Its high tensile strength makes it particularly suitable for heavy-duty vehicles and those that require substantial load-bearing capabilities. Despite its heavier weight compared to aluminum, advances in steel production, such as high-strength low-alloy (HSLA) steel, have reduced its weight slightly, maintaining strength while improving efficiency. Steel's durability makes it a reliable choice for many automakers, ensuring safety and stability.

When looking at technological innovations, carbon fiber emerges as an exceptional candidate for control arm material. Despite its higher cost, carbon fiber’s ultra-lightweight and incredibly strong properties provide superior performance benefits. Its use is primarily seen in high-end, performance-oriented vehicles where maximizing power and speed are pivotal. Besides, carbon fiber inherently dampens vibrations, contributing to a smoother driving experience.
Polyurethane, although not often used alone for entire control arms due to its flexible nature, is often used in bushings within control arms. This material adds notable performance improvements by providing a flexible yet resilient connection, reducing noise, and mitigating vibrations effectively. In terms of customization, polyurethane offers various durometers, or hardness levels, allowing for specific tuning according to different vehicular needs.
control arm material
Each of these materials has its specific applications, determined by balancing factors such as safety requirements, cost constraints, and performance aspirations. For instance, luxury sports cars prioritize aluminum or carbon fiber due to their weight-saving properties, while larger SUVs and trucks might opt for steel to cater to heavy lifting.
In the landscape of product development and innovation, partnerships between automotive manufacturers and material scientists are vital. These collaborations ensure that new, hybrid materials can be developed, combining the best properties of existing ones. Moreover, as sustainability becomes ever critical, advances in recyclable and eco-friendly composites for control arms are receiving significant attention.
Keeping these aspects in mind, those in the automotive industry must regularly re-evaluate the materials used in their products. The right choice involves a thorough analysis of the vehicle's intended use, market positioning, and long-term performance goals. By critically evaluating these criteria, manufacturers can make informed decisions that align with contemporary demands for efficiency and sustainability while enhancing their cars' reputation for reliability and innovation.
Ultimately, staying ahead in automotive design with the right control arm material isn’t merely about following current trends.
Industry experts must predict future technological and environmental transformations to stay competitive. Encouraging ongoing educational pursuits and practical experimentation within the field champions innovation.
In summary, the ideal control arm material is not universally fixed but varies with an application’s needs. Through informed selections and continuous material evaluation, automakers can ensure their vehicles remain at the forefront of performance and reliability, meeting and exceeding the standards set by the ever-evolving global car market.